Managing risk is key to safety in any work environment. Understanding, assessing and managing hazardous substances, from air monitoring to PPE, means creating a safe space to work as well as complying with health and safety law.
Managing Hazardous Substances
Managing risk is key to controlling the potentially harmful effects of hazardous substances in the workplace
Understanding The Risks
Prior to prescribing the appropriate respiratory protective equipment (RPE), it’s important to manage hazardous substances and first consider whether they can be reduced or controlled. Identifying materials which may create airborne dusts, toxic gases or harmful fumes should be part of a risk assessment so appropriate control measures can be implemented to mitigate these potential hazards and protect employees from respiratory diseases.
Work-related Respiratory Illnesses
Many people working in multiple industries are exposed to hazardous substances by inhaling dusts, mists, fumes and vapours. Thousands of workers are not aware of the long-term damage this can cause and can take years after the exposure before any symptoms of ill health become apparent.
Breathing in hazardous substances on a regular basis, over a long period of time can seriously impact a person’s health and can have life-changing or even life-threatening implications.
Identifying and Assessing The Risk
Identifying the materials and substances used within the workplace will help determine the control measures that must be in place before the substance is used. Material safety datasheets (MSDs) contain information about the substances that make them up, its uses, hazard identification and human health risks as well as advice on exposure controls and personal protection.
Before carrying out any work, a risk assessment should identify any risks involved and the types of control measures that should be adopted.
Being proactive is key to any risk assessment. In the first instance you must identify what potentially hazardous material is being used followed by who could potentially be affected. Consideration should be given to whether the public or other people who work or live in or around the space may be affected.
Things to consider:
- What the task involves, including equipment and tools
- The environment / work area
- How long the task will take
- Frequency of the task throughout the day
Employers have a responsibility to take reasonable steps to prevent harm coming to anyone in and around the workplace. The person conducting the risk assessment also needs to be trained and competent to do so.
Workplace Exposure Limits (WELs)
Hazardous Substances have a Workplace Exposure Limit (WEL) which must not be exceeded. WELs are British occupational exposure limits measuring the concentration of hazardous substances in the air, averaged over a period of time and is referred to as time weighted average (TWA).
Used to help protect the health of workers, substances that have been assigned a WEL are subject to the requirements of COSHH. These regulations require employers to prevent or control exposure to hazardous substances.
To find out more and view the list of substances that have been assigned a workplace exposure limits, view the EH40/2005 workplace exposure limits.
Air Monitoring
Without air monitoring it is impossible to understand how much contaminant is in the air. Air monitoring and measurement will help identify any airborne hazardous issues in the workplace, assess the risk to workers' health and confirm that current control measures are working. Knowing this also provides the confidence to recommend the correct RPE.
Under Reg 10 of the COSHH Regulations 2002, employers must ensure that workplace air monitoring is undertaken when working with hazardous substances to ensure adequate control.
Arco Professional Safety Services can help you calculate the airborne concentrations of your workplace and recommend realistic solutions to reduce the exposure to your employees. By assessing their health from exposure, both in the short and long-term, will help ensure your business is meeting its legislative requirements to protect people by implementing 'adequate control' measures.
Controlling The Risks
Once the hazard has been recognised, reasonably practicable control measures must be developed depending on the risk and applied to each task to ensure the health and safety of your employees and those around.
- Eliminate the use of harmful substances and remove the hazard in its entirety
- Consider substitution and using a safer material. MSDs will highlight the content which may help you come up with an alternative
- Use engineering controls that work to isolate or reduce exposure of the substance such as less powerful tools, introducing water or bringing in on-tool dust extraction
- Ensure there are a set of administrative controls and that employees are competent to use the control measures put in place. Relevant training and shift rotation can help reduce workers' exposure to hazardous substances
- If these methods do not prevent or control the exposure, PPE in form of Respiratory Protective Equipment (RPE) will need to be issued. Remember, face fit testing is required for all tight-fitting facepieces
As a priority, before the work commences, you will need to identify whether the proliferation of airborne substances can be controlled or even prevented altogether. In accordance with good occupational hygiene practice, the risk assessor should adopt the hierarchy of control to reduce the risk:
Carrying out regular health surveillance on workers will check that control measures are working. By monitoring workers' health, the surveillance can identify early signs of ill-health and by acting on the results helps ensure that adequate control measures are being followed.
Equipment
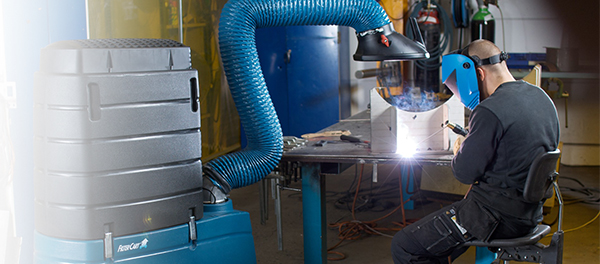
Local Exhaust Ventilation (LEV)
Work that produces hazardous airborne contaminants is often a health risk to everyone in the workspace. LEV is an effective engineering control method but it’s vital to select the right equipment, then maintain and operate it properly.

Our Range
Our extensive range of respiratory protection equipment offers protection against a variety of hazards, is designed to suit a variety of work situations and available in a variety of styles to match the requirements of the wearer.
Ways of Working
Managing hazardous substances can also be achieved by the way a business works through its operating procedures, supervision and training. It can also include an organisations' emergency procedures, decontamination and permits to work for tasks such as maintenance.
The right combination of equipment and ways of working is crucial for reducing exposure and controlling the risk. However, unless used properly, control measures will not work. That's why it is important for your workers to:
- Wear any necessary PPE
- Use control equipment
- Follow hygiene procedures
- Warn supervisors if anything appears to be wrong
By testing these control measures and equipment on a regular basis makes sure that they work properly. Keeping records of examinations and repairs for at least five years can help to identify any trends or variations in equipment deterioration. The right combination of equipment and ways of working is crucial for reducing exposure. If not used properly, these control measures will not work.
More from Arco
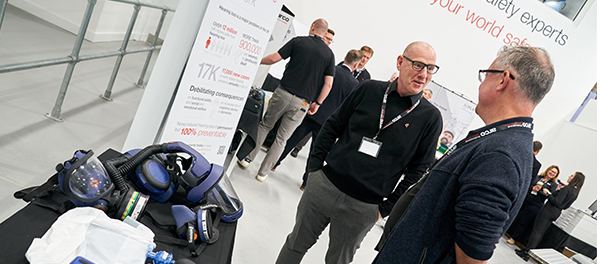
Advice and Support
From consultancy and risk management to specialist respiratory services such as expert training and equipment maintenance, our Arco Professional Safety Services can offer a range of advice and support to help implement a respiratory programme.
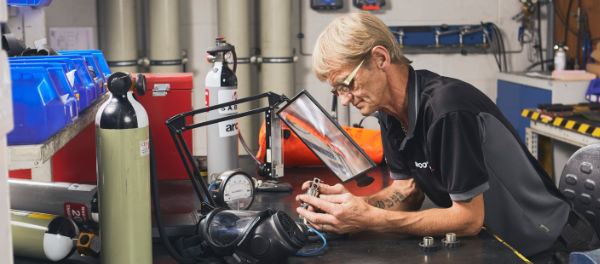
Safety Standards
By law, employers are required to control substances that are hazardous to health under Control of Substances to Hazardous Health regulations (COSHH). Any RPE provided must be tested to the relevant European standards and carry a CE mark.